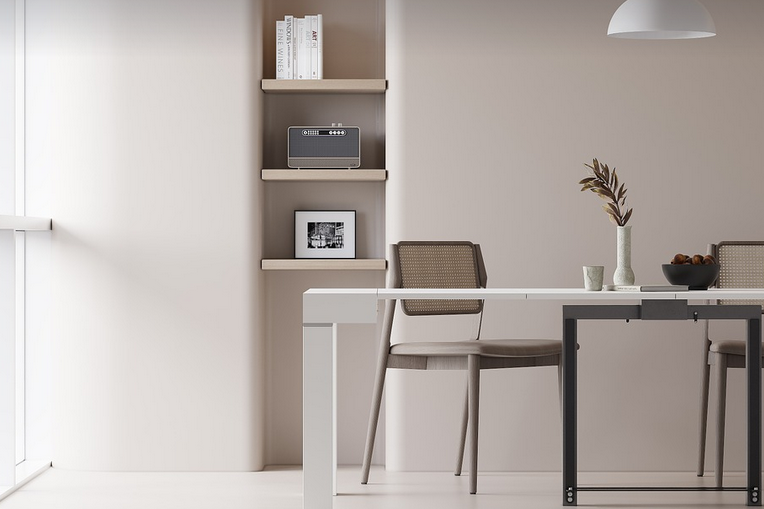
Warehouse Quality Control: Your Guide To Keeping Products Perfect
What Exactly Does a Warehouse Quality Control Job Entail?
Working in a warehouse often conjures up images of massive stacks of products and endless conveyor belts. But behind the scenes, a crucial element ensures those items reach customers’ hands in perfect condition: quality control. This job involves ensuring that every product leaving the warehouse meets specific standards and regulations before it heads out to its final destination.
Imagine yourself as an inspector for each incoming shipment. You meticulously check each box for any damage, making sure the correct quantity of products is present. You also ensure that the sizes and colors match the specifications outlined in the purchase order. Sometimes, this involves a closer look at packaging – checking for any signs of tampering or leaks. Your focus is on identifying imperfections before they cause problems down the line. From fragile items like electronics to more robust goods like building materials, your role requires keen attention to detail.
Quality control in a warehouse isn’t just about inspecting products; it also involves processes and tools. You might be responsible for setting up quality checks, documenting results using spreadsheets, or even training colleagues on proper inspection techniques. You’ll play a pivotal role in maintaining the integrity of the company’s inventory and ensuring its smooth transition from warehouse to customer.
These roles often require a keen eye for detail and the ability to quickly identify discrepancies. While some tasks might be repetitive, the overall impact on the business is significant.
Let’s dive deeper into the key responsibilities of a warehouse quality control expert:
Key Responsibilities of a Warehouse Quality Control Specialist
A day in the life of a quality control specialist might include these crucial tasks:
**1. Inspection:** This is arguably the core task. You’ll meticulously examine incoming shipments for any damage, defects, or discrepancies between order details and delivered items.
**2. Documentation:** You’ll be responsible for diligently recording your inspection findings in detailed logs and spreadsheets. This ensures accurate tracking of quality issues and helps identify trends affecting product integrity. Maintaining these records is crucial for compliance with industry standards and internal audits.
**3. Packaging Verification:** Ensuring the correct packaging, labeling, and storage conditions are met. This involves checking for proper sealing and identifying any packaging discrepancies that might affect product safety and handling during transit.
**4. Product Sorting and Labeling:** You’ll often play a role in separating damaged items or those requiring specific attention from those ready for shipment. This involves accurately labeling and categorizing products, ensuring smooth allocation to various storage areas
**5. Training and Supervision:** You might be responsible for training new employees on quality control procedures and best practices. Your expertise could encompass everything from proper inspection techniques to document management and reporting.
**6. Continuous Improvement:** A key aspect of your role is identifying ways to improve current processes and workflows. This can involve suggesting changes, streamlining the inspection process, or even implementing new tools for quality control.
**7. Problem Solving:** You’ll be a problem solver in many instances. If you notice a recurring issue with a certain product type, you might investigate its root cause to prevent similar problems in future shipments.
These responsibilities are often multifaceted and require flexibility and adaptability.
What Skills Do I Need for a Warehouse Quality Control Job?
You don’t need a university degree to excel in this role, but certain qualities can make your journey smoother.
**1. Attention to Detail:** Meticulousness is essential. You must be able to spot even the smallest defects and discrepancies.
**2. Analytical Skills:** The ability to think critically about product inspection data and identify recurring patterns. This helps you pinpoint potential issues before they impact customer satisfaction.
**3. Communication Skills (Verbal & Written):** Your role often involves communicating with colleagues regarding quality observations, raising concerns, or relaying information to upper management.
**4. Problem-Solving Abilities:** Troubleshooting and resolving quality problems is a crucial part of the job. You’ll need to apply critical thinking to identify root causes and implement effective solutions.
**5. Time Management Skills:** Balancing multiple inspection tasks, documentation, training, and problem resolution requires strong time management skills. The ability to stay organized and prioritize work effectively is vital.
**6. Mechanical Aptitude:** Understanding how products are packaged and handled can help you identify potential damage or mishaps during storage and transportation.
**7. Familiarity with Industry Regulations:** Understanding relevant quality control standards, certifications, or safety regulations specific to your industry will be valuable.
Why Choose a Warehouse Quality Control Career?
Beyond the technical expertise, there are several compelling reasons to consider a career in warehouse quality control:
**1. Making a Direct Impact:** You’ll be playing an active role in ensuring that products reach customers with the expected level of quality and safety.
**2. Learning Valuable Skills:** Develop a comprehensive understanding of product inspection, documentation, and process optimization. This can translate into skills applicable across various industries.
**3. Evolving Profession:** The demand for skilled warehouse professionals is constantly growing, offering promising career growth opportunities in the logistics and supply chain sectors.
**4. A Rewarding Career Path:** You’ll be contributing to a company’s success by ensuring product quality, leading to higher customer satisfaction and brand reputation.
**5. Opportunities for Advancement:** The skills you acquire can open doors to leadership roles in managing quality control teams or even starting your own consulting business in this field.
Warehouse Quality Control: more than just inspecting products; it’s a career dedicated to ensuring excellence at every step of the supply chain, from warehouse floor to customer’s hands.