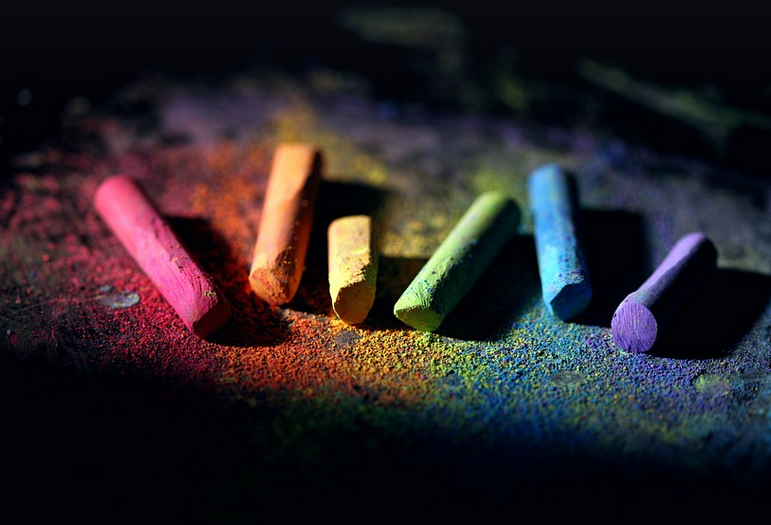
Understanding True Stress: Beyond Engineering Stress
What is Engineering Stress?
Imagine you’re working on a challenging project, maybe designing a bridge or building a super-durable spacecraft. You need to make sure your materials can withstand the immense pressure they might face under tension.
This “pressure” – the force acting on a material from a certain direction – is what we call “engineering stress.” Engineering stress is a fundamental concept in engineering and mechanics, representing the internal forces within a material or component.
In simple terms, it’s the measure of how much a material is being squeezed, stretched, or bent.
Why Does Engineering Stress Matter?
Engineering stress tells us more about a material’s strength and potential for failure. By calculating engineering stress, engineers can make informed decisions regarding materials selection, design specifications, and load limits.
It helps predict the performance of materials under various conditions, such as temperature changes or varying loads.
The Limitations of Engineering Stress
While engineering stress provides valuable insights into a material’s behavior, it has some limitations. It doesn’t tell us the full story about how a material might actually fail.
Here’s why: Imagine you were to compare a bridge’s resistance to a car crash. Engineering stress would focus on the tension forces that might be exerted during the collision. However, this doesn’t account for the impact’s energy transfer, or the potential damage caused by sudden changes in pressure.
Here’s the key: Engineering stress looks at the “forces” acting upon a material, but it doesn’t tell us about *how* these forces are actually impacting the material.
Enter True Stress
To understand the true story of how materials behave under stress, engineers use another important concept called “true stress.” It offers a more complete picture by considering not only the applied force but also the strain and deformation of the material.
True stress is defined as the ratio between the internal forces within the material (like microscopic vibrations) and the cross-sectional area of the material. Imagine a tiny rubber band being stretched; as you stretch it, the stress on the material changes from just pulling to also stretching and bending.
True stress takes into account these nuances of deformation and provides a more realistic measure of how much a material can endure before it yields.
Why Is True Stress Important in Real-World Applications?
In today’s world, engineers face complex challenges like designing airplanes, constructing skyscrapers, or developing medical devices. These projects require materials that can resist intense stress and strain while still maintaining their structural integrity.
True stress helps us understand the actual response of the material to these stresses. It can help predict failure points and optimize designs for durability. This information is crucial in ensuring safe, functional products and structures.
The Impact on Materials
The difference between engineering stress and true stress has significant implications for material selection and design.
For instance, if you’re designing a bridge with heavy loads, engineering stress might be sufficient to calculate the maximum load capacity. However, true stress represents the actual deformation and damage the material experiences under those extreme conditions.
Conclusion: A Deeper Understanding
Converting engineering stress to true stress provides a more comprehensive understanding of materials’ behavior and performance in real-world applications. It goes beyond simple force calculations and offers insights into how a material responds to strain and deformation. This deeper knowledge allows engineers to design safer, stronger, and more reliable structures and devices.